I was looking for the CNC machine with tool changer quite a while and finally I have found this one here. This is a fantastic machine tool for mold making, and the automatic tool changer kit really saves my time a lot.
CNC Molding Machine with Automatic Tool Changer
A CNC molding machine is an automatic computer-controlled mold making machine for precision milling & cutting textures, intaglios, and reliefs into metal molds. Now the best CNC mold making machine for sale at affordable price.
- Brand - STYLECNC
- Model - ST6060C
- Supplity - 360 Units in Stock Available for Sale Every Month
- Standard - Meeting CE Standards in Terms of Quality & Safety
- Warranty - One-Year Limited Warranty for Entire Machine (Extended Warranties Available for Major Parts)
- 30-Day Money Back Guarantee for Your Purchase
- Global Logistics and International Shipping for You
- Free Lifetime Technical Support for End-Users & Dealers
- Online (PayPal, Trade Assurance) / Offline (T/T, Debit & Credit Cards)
What is a CNC Molding Machine and How Does it Work?
A CNC moulding machine is an all-purpose precision CNC machine that integrates a computer numerical control technology in its cutting and milling operations. It is also identified as a Computerized Numerical Control Molding Machine, CNC mold-making machine, and Computerized Numerical Control Mold Milling Machine. Just like other ordinary CNC machine tools, through the use of the G code, the CNC system acts to command the activity to fulfill the automation of the process of cutting and milling. It is suitable for industrial mold manufacturing, art relief carving, personalized seal nameplate production, decoration industry, and printed circuit board processing. In addition, according to the teaching needs of colleges and universities, an open control system is adopted. Through different control connections and software control, a semi-closed loop and full-closed loop control system can be formed.
CNC molding machines can process text, patterns, textures, small complex surfaces, thin-walled parts, small precision parts, and irregular artistic reliefs. These objects are characterized by small size, complex shapes, and fine finished products.
In terms of processing technology, due to the small and complex engraving area, the CNC molding machine uses small mill cutters below 6.0mm for fine processing. It is of great significance for the required batch product processing.
The principle of a CNC molding machine is high-speed milling. Compared with traditional CNC machining, CNC routing is similar to high-speed milling, which is vividly called the processing method of "eat less and run faster".
The use of CNC molding machines has low labor intensity, a high degree of automation, and less dependence on operators. The control system automatically controls the tool movement of the CNC mold milling machine according to the processing instructions to complete the milling task, which greatly reduces the labor intensity. This highly automated process enables production to be significantly less reliant on the skills of traditional hand-carving operations.
Features of CNC Molding Machine with Automatic Tool Changer
1. It is the product of the combination of numerical control technology and the engraving and milling process. It is a kind of multi-functional CNC machine. Similar to the ordinary numerical control machine, our metal engraving machine price realizes the carving, and the milling processing automation through that numerical control system controls the engraving and milling machine movement according to process procedure code.
2. Stable and rigid structure: With the gantry type bed and table in one, it is not only good rigidity but also no installation error for both. The precision will not be affected even if being used for a long time.
3. It is a kind of fully enclosed design, it adopts an external circulating cutting oil processing way. The machine body is fully cast with a stable structure and great weight-bearing ability.
4. The machine has been equipped with an accurate bidirectional ball screw of a famous brand, Taiwan square rail, and accurate bearing with strong rigidity and high dynamic accuracy. It is also equipped with a Japan YASKAWA AC servo motor with high accuracy and high power making the amplitude smaller and three-axis more stable.
5. The CNC mold milling machine is equipped with an automatic tool changer system.
Advantages of CNC Molding Machine with Automatic Tool Changer
1. Gantry structure: Whole cast-iron structure, steady structure, high rigidity, precision 0.01mm. The double column is the whole part, greatly increasing machine rigidity.
2. Adopt high-speed water cooling variable frequency motor, big torque, strong cutting, high-frequency,long-lifetime, can be a long time continuous working.
3. Cooling system: Oil circulating oil cooler for spindle, cooling workpieces with water or oil in the tank, or atomization liquid through or spray nozzle.
4. Quality assurance: For each device before leaving the factory, we will test the cue with a laser interferometer.
5. Servo motor and drives: from Japan with high precision and long life.
6. HIWIN linear guide: made in Taiwan, used for linear reciprocating stadium.
7. Three axes all use German ball screws and Taiwan linear orbits to make sure accuracy and reposition precision.
8. Functional and easy-to-operate control system made by Taiwan SYNTEC with high performance and competitive price.
9. Adopt table movement to keep stable and high precision.
10. Enclosed work space ensures safe and contamination-free work.
11. Automatic tool changing system with 4 tools.
Technical Parameters of CNC Molding Machine with Automatic Tool Changer
Model | ST4040C | ST6060C |
Working Table size | 400mm×400mm | 600mm×600mm |
X/Y/Z Axis Movement | 450mm×450×250mm | 600mm×600mm×300mm |
XYZ movement Accuracy | ±0.01/300mm | ±0.01/300mm |
XYZ Repetition Accuracy | 0.005mm | 0.005mm |
Flatness Error of Working Table | ≤0.03mm | ≤0.03mm |
XY Verticality Error | 0.02mm | 0.02mm |
Media Height | 50 – 300mm | 50 – 350mm |
Gantry Width | 740mm | 820mm |
Max Loading Weight | 300kg | 350kg |
Pressure Deformation of Working Table | <0.02mm(300kg) | <0.02mm(300kg) |
Spindle Power | 2.2KW(Optional 5.5KW) | 2.2KW(Optional 5.5KW) |
Tool holder | BT20 (Optional BT30) | BT20 (Optional BT30) |
Spindle rotate speed | 5000-24000rpm | 3000-18000rpm |
Max movement speed | 15m/min | 12m/min |
Total power | 7.5KW | 13.5KW |
Motor | Yaskawa Servo Motor | Yaskawa Servo Motor |
Power supply | 380V ± 10%50Hz | 380V ± 10%50Hz |
CNC Molding Machine Applications
The CNC molding machine is applicable to carve, mill, cut, and drill most materials, including but not limited to copper, aluminum, steel, iron, brass, wood, foam, and plastics. It finds its massive applications in injection mold, automotive, ironware mold, shoe mold, drop mold, metal molds, clock parts, copper electrodes, zinc electrodes, metal electrodes, metal crafts, metal arts, jewelry, jade, dental crown, among other molding industries. This machine is specially designed for batch machining molds, watches, eyeglasses, panels, brands, badges, outside surface sleeking, three-dimensional graphics, and words. It is easy for this molding machine to provide 2D or 3D relief on various materials.
CNC Molding Machine Projects
CNC Molding Machine Samples
Comparison of CNC Molding Machines with and without Automatic Tool Changers
This will be important in understanding how each option will affect efficiency and precision as well as the overall workflow when deciding on a CNC molding machine with or without an ATC. Here's a breakdown of the key differences.
Efficiency
CNC molding machines with ATC minimizes shutdowns to a very low level, as the tool changing process is automated. Therefore, machines can work non-stop without requiring any intervention from an operator, hence fastening the production cycles. Machines without an ATC need manual tool changes, increasing downtime and reducing production rates.
Precision and Accuracy
Machines with ATC offer higher precision since the tools are automatically swapped with consistent alignment, ensuring accuracy across production runs. Manual tool changes can introduce slight errors in tool alignment, which may affect the consistency and quality of the finished parts.
Operator Involvement
By nature, ATC offers a machine to operate largely unaided by man, thus allowing minimal operator errors, while workers can attend to other tasks. However, without an ATC, machines are much more hands-on for operators in changing their tools, and thus it could imply interruptions and mistakes.
Cost
CNC molding machines with ATC generally have a higher upfront cost due to the advanced technology. However, the increased production speed and reduced labor costs typically offset the initial investment. On the other hand, machines without ATC are more affordable initially, but they incur higher long-term operational costs.
Maintenance Tips for CNC Molding Machines with ATC
Maintaining CNC molding machines with an automatic tool changer (ATC) is crucial for ensuring smooth operation, and longevity, and minimizing costly repairs. Here are some essential maintenance tips:
• Regular Cleaning: Keep the machine and its components clean, particularly the tool changer mechanism. Dust, dirt, and debris can cause friction and thus accelerate wear on the ATC. The cleaning of a tool holder, a tool magazine, and all the moving parts should be regular to ensure smooth operation.
• Lubrication of Moving Parts: Regular lubrication of the machine's moving parts is done to reduce friction and wear. The list includes the tool changer's mechanical parts, rails, and spindles. Proper lubrication is done to ensure smooth movement that prolongs the system life.
• Check tool changer for wear or misalignment: Calibrate the ATC regularly to ensure it can actuate correctly. Inconsistent alignment can cause improper tool changes, resulting in low machining accuracies and productivity.
• Air and Fluid Levels: Most of the ATC machines use compressed air and hydraulic fluids. Keep these levels maintained and ensure that leak-free systems are provided. Low air pressure or insufficient fluid levels may be responsible for malfunctioning of the tool changer.
• Software Updates: Regular updates on the machine's software are necessary to avoid operational errors or issues with the ATC system. Bugs in software or outdated firmware will reduce performance and create unnecessary downtime.
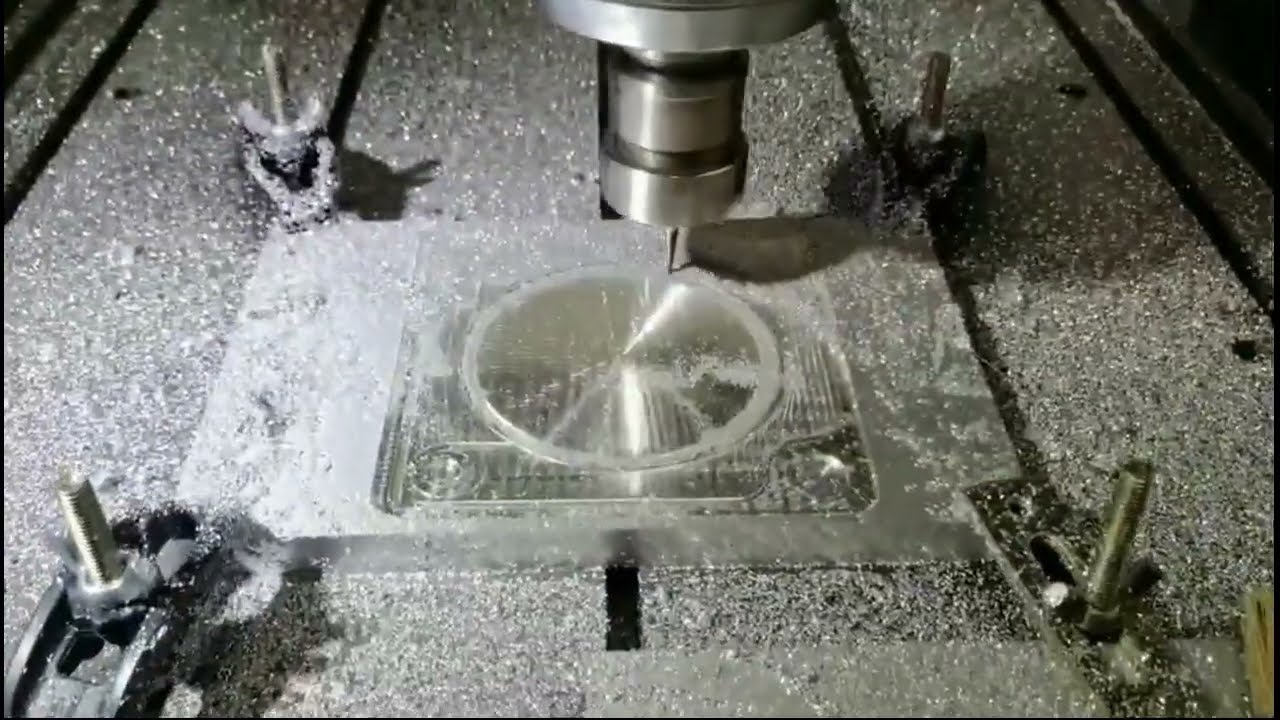